Electric vehicle coolant corrosion simulation test bench DW512
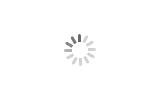
- DOOWAY
- CHINA
- 30 days
- 5 sets per month
Instrument Overview
With the rapid expansion of the new energy vehicle market, vehicle antifreeze has also ushered in unprecedented development opportunities. The strong development momentum of new energy vehicles will have a profound impact on the coolant industry. With the popularization of new energy vehicles and the advancement of technology, the performance and quality requirements for coolants will continue to improve, bringing new challenges and opportunities to the coolant industry.
New energy vehicles have extremely high requirements in terms of temperature control and management of in-vehicle heat sources, mainly involving heat source components such as batteries, controllers and motors. At present, liquid cooling has become the mainstream heat dissipation method for new energy vehicles because it is not only safe, but also has significant heat dissipation effect. Compared with traditional fuel vehicles, new energy vehicles have significantly increased the use of coolant. The safety and reliability of electric vehicle coolant are crucial to ensuring the normal operation of electric vehicles. The corrosion test bench for electric vehicle coolant developed by our company can play a positive role in promoting in many fields, improving product quality and protecting consumer rights and interests.
The test bench can simulate the actual operating conditions (temperature, flow and loop environment) of the coolant in typical application scenarios of automobile operation, automatically operate during the test time, and automatically monitor the pH value, conductivity and other parameters of the coolant during operation. Change status and trends. Samples can be taken for ion composition analysis. The test bench can solve problems such as complicated manual steps, many human factors, and inaccurate data during the test process, improve work efficiency and ensure the safety of testers.
Instrument parameters
The simulated use temperature of coolant is 80±2℃ (adjustable from room temperature to 95℃);
Temperature control accuracy: 0.5℃;
Loop coolant flow: 5~30L/min±0.25 L/min;
Loop pressure <35kPa;
Simulated operation test time: can be set, the factory setting is 1064± 2H;
pH meter: Range range 0~14, accuracy 0.1;
Conductivity meter: range 0.0~100μS/cm, accuracy 0.1μS/cm;
Empty weight of main engine: 160kg;
Power supply voltage: 220VAC,50HZ, maximum power: 3kW;
Host size (W*D*H): 1500*1020*2200 mm.
Functional properties
The test bench can be optionally connected to battery cooling plates, electronic cooling boxes and motors, with rich interfaces;
The bench can realize automatic sample injection and automatic sample layout;
Equipped with an online pH meter and an online conductivity meter, measure the pH value and conductivity value of the coolant at a fixed time every day, and the change trend curve of the two can be observed on the monitoring screen of the controller;
Set a sampling valve to take samples regularly for offline testing of freezing point value or ion composition analysis of samples;
After the test, the controller can directly form a test report, including the change trend curve of the coolant pH value and conductivity;
Because the test process of the simulation bench is relatively long, the simulation bench adopts fully automatic technology, and no one is on duty during the entire test process;
The test bench is equipped with warning lights to remind the test stage and fault alarm prompts respectively;
Mechanical parts in the bench are standardized and universalized, and pipeline components, functional parts and sensors meet functional and precision requirements while meeting high corrosion resistance;
The bench control system adopts modular design, and the control components are all made of standard and mature industrial automation products to ensure stability and reliability;
The human-computer interactive design of the bench application software monitors the operation of the coolant in the loop by simulating dynamic images; monitors the temperature, flow and pressure of the coolant in real time; displays the current pH value, conductivity and its freezing point based on the measurement results of online sensors; test time progress information; provides timely alarm information when the data exceeds the preset extreme value;
The application software adopts touch screen operation, and the test information setting supports Chinese input.