Corrosion simulation test bench for proton exchange membrane fuel cell coolant DW510
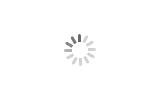
- DOOWAY
- CHINA
- 30 days
- 5 sets per month
The test bench can simulate the actual operation of coolant (temperature, flow rate and environment) in the most typical application scenarios of proton exchange membrane fuel cell (PEMFC), and run automatically in a long simulation time, and the loop can automatically monitor the change and trend of pH value, electrical conductivity and freezing point during operation, and can sample for ion composition analysis. The test bench will solve the problems of complicated manual steps, many human factors and inaccurate data in the test process, and improve the work efficiency and ensure the test personnel.
DW510 simulates the application scenario of proton exchange membrane cell as fuel cell generator according to its practical application environment, which is also the largest, most meaningful and most typical application scenario of proton exchange membrane fuel cell at present and in the future.
Function Features
u The test bench can be directly connected to the fuel cell, or the corrosion effect of coolant on a single bipolar plate can be tested by an independent test box.
u The bench can realize automatic sample injection and facilitate emptying.
u Equipped with on-line pH meter and on-line conductivity meter, the pH value and conductivity value of coolant are measured at a fixed time every day, and the trend curve of them can be observed on the monitoring screen of the controller.
u Set up a sampling valve to sample regularly for offline test samples for freezing point value or ion composition analysis.
u After the test, the controller can form the test report directly, including the trend curve of coolant pH value, electrical conductivity and freezing point.
u Because the simulation bench test process is relatively long, the simulation bench mining.
u The full automatic technology is used to realize unattended during the whole test process.
u The test bench is equipped with warning lights to indicate the test stage and fault alarm respectively.
u The mechanical parts in the bench are standardized and universal, and the pipeline components, functional parts and sensors meet the requirements of function and precision, while meeting the high corrosion resistance.
u The bench control system adopts modular design, and the control components are selected with standard and mature industrial automation products to ensure stability and reliability.
u The human-computer interaction design of the bench application software monitors the operation of the coolant in the loop by simulating dynamic images; real-time monitors the temperature, flow rate and maximum pressure of the coolant; displays the current pH value, conductivity and freezing point data according to the measurement results of the on-line sensor; the progress information during the test; when the data exceeds the preset extreme value, timely alarm information is given.
u The application software is operated by touch screen, and the test information setting supports Chinese input.
u The overall design of the platform adopts the design of unattended cabinet, which is convenient to install and has complete safety warning facilities.
Technical Specifications
u Fuel cell coolant simulation temperature 90 ±1 ℃ (room temperature ~ 95 ℃ adjustable).
u Temperature control precision: 1 ℃.
u Loop coolant flow rate: 5~10L/ min ±0.25L/min.
u Circuit pressure < 35kPa.
u Simulation test time: can be set, factory setting 1176 ±1H.
u PH meter: range 014, accuracy 0.1,
u Conductivity meter: range 0.0100 μ S / cm, accuracy 0.1 μ S / cm.
u Host size (W*D*H): 600*500*1600mm.
u Main engine empty weight: 350kg.
u Power supply voltage: 220VAC 50Hz, maximum power: 5kW.